Background
Starch syrup is a kind of sugar syrup which is mainly produced from agricultural products such as corn, wheat, rice, potatoes or cassava (the most important one is corn starch), by technology of hydrolysis and transformation of biotechnology. In modern industry, enzymatic process is widely used to produce starch syrup such as glucose/fructose/maltose syrup, maltodextrin, etc. All these processes mainly include: making starch slurry, liquefaction( /saccharification ), clarification/filtration, decolorization, IE demineralization, concentration, among which, clarification/filtration of liquefaction/saccharification liquor is one of the key steps, and the filtration effect directly affects the post-refining cost and product quality.
Traditional Process
The liquefaction/saccharification liquor contains a certain amount of impurities such as proteinaceous matter, fat, unhydrolyzed starch, polysaccharides, enzyme fragments and other impurities, which increase the color of the liquefaction/saccharification liquor and the subsequent refining difficulty, degrade the product quality, and must be removed. Traditional filtration technology for liquefaction/saccharification liquor mainly includes Filter Press Filtration, RVDF (Rotary-Drum Vacuum Filter), with perlite/ diatomaceous earth in it. For these filtering techniques, the filter residue containing filter aid or activated carbon can’t be further exploited such as animal feed, and only can be discarded as solid waste which is not environmentally friendly. At the same time, frequent replacement of filter aids increases production costs.
CRM Membrane Process
In a very short duration, cross flow membrane filtration has become a mainstream process unit operation in the Starch & Sweetener industry. The process eliminates use of diatomaceous earth (kieselgur) in rotary vacuum filters, while at the same time producing a superior quality product. Ceramic membrane by its versatility and unique separation techniques have gained wide acceptance. Membrane filtration find its niche either by itself or in combination with other more established technologies. TFT has developed a starch hydrolysate clarification ceramic membrane which has superior performance in starch hydrolysate filtration and purification with stable flux rate and high impurity removal rate. In order to determine the flux, permeate quality and other operational parameters, TFT offers its customers laboratory tests and on-site tests. For this purpose, TFT has developed all kinds of small filtration units for meeting the demands of customers.
Process Diagram
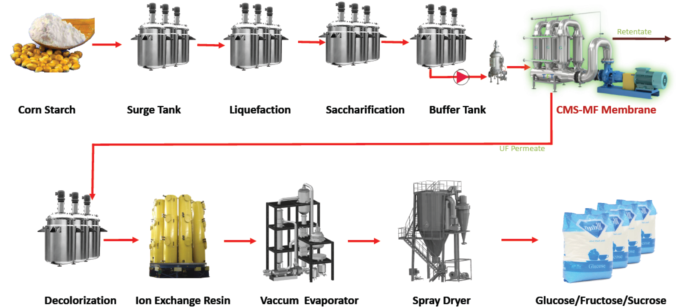
Process Advantages
Compared with traditional filtration technology, ceramic membrane cross flow filtration has many advantages: A reliable process, already successfully applied in other starch plants A green economical technology without filter aids (perlite/diatomite),less waste discharge A reliable filtration for syrup clarification with less product loss Good quality of filtrate syrup with high light transmittance Membrane filtrate syrup can go to resin demineralization directly, no need of activated carbon decoloration Less contamination to Ion exchange resin and prolong the resin life Less CPEX and OPEX Easy maintenance, Low labor cost Compact design with less footprint.